Procurement Quality Control
Responsible for RRP* quality, cost, and delivery
The staffs of Procurement Quality Control are responsible for the procurement of electronic and mechanical components necessary for the manufacture of RRP* devices, as well as the quality control of devices and cartridges manufactured by overseas subcontractors. Compared to cigarettes, RRP* are a relatively new type of tobacco product. Therefore, the R&D Group has established a procurement and quality management system for RRP* from scratch. The team responsible for procurement and quality control is still young and has a short history. However, as demand for RRP* is increasing, this team is directly involved in all aspects of cost, quality, and delivery, and play an extremely important role in delivering high-quality products to consumers in a timely manner.
*Reduced-Risk Products: Products with the potential to reduce the health risks associated with smoking
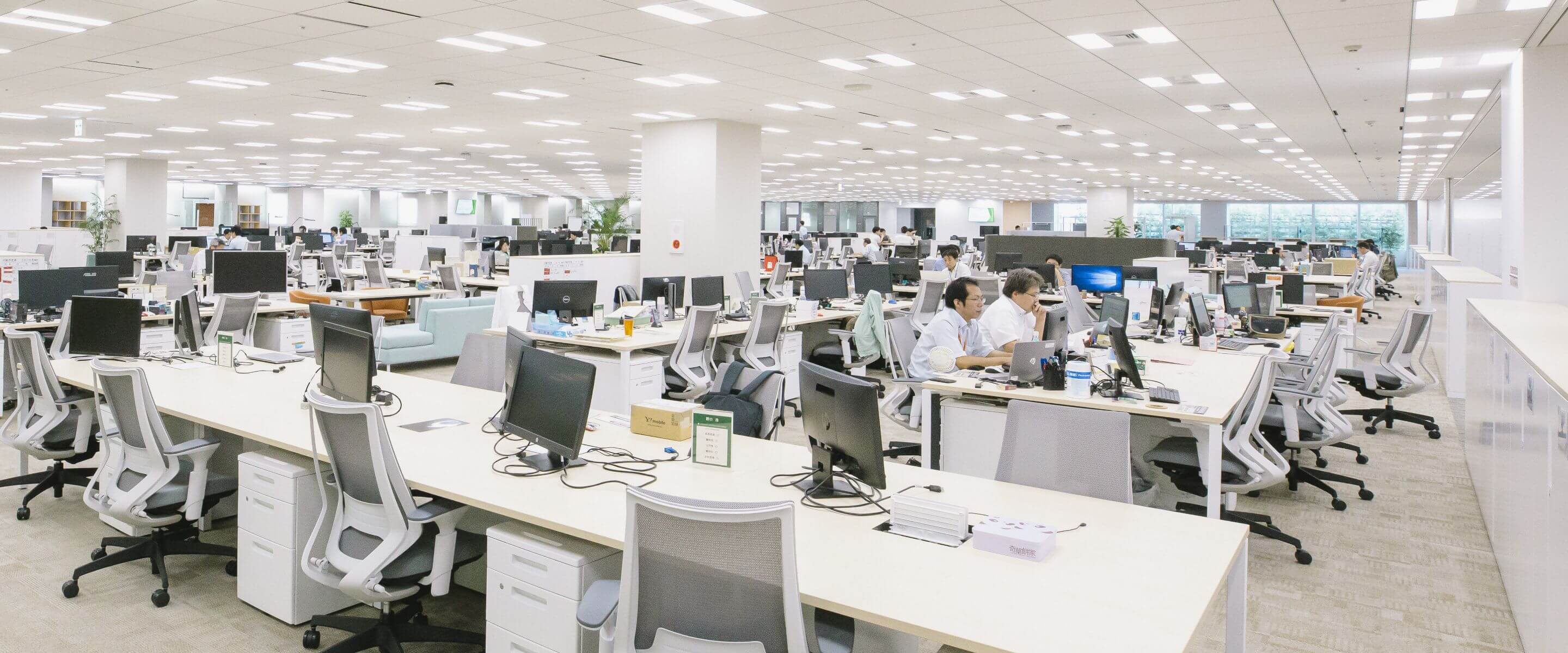
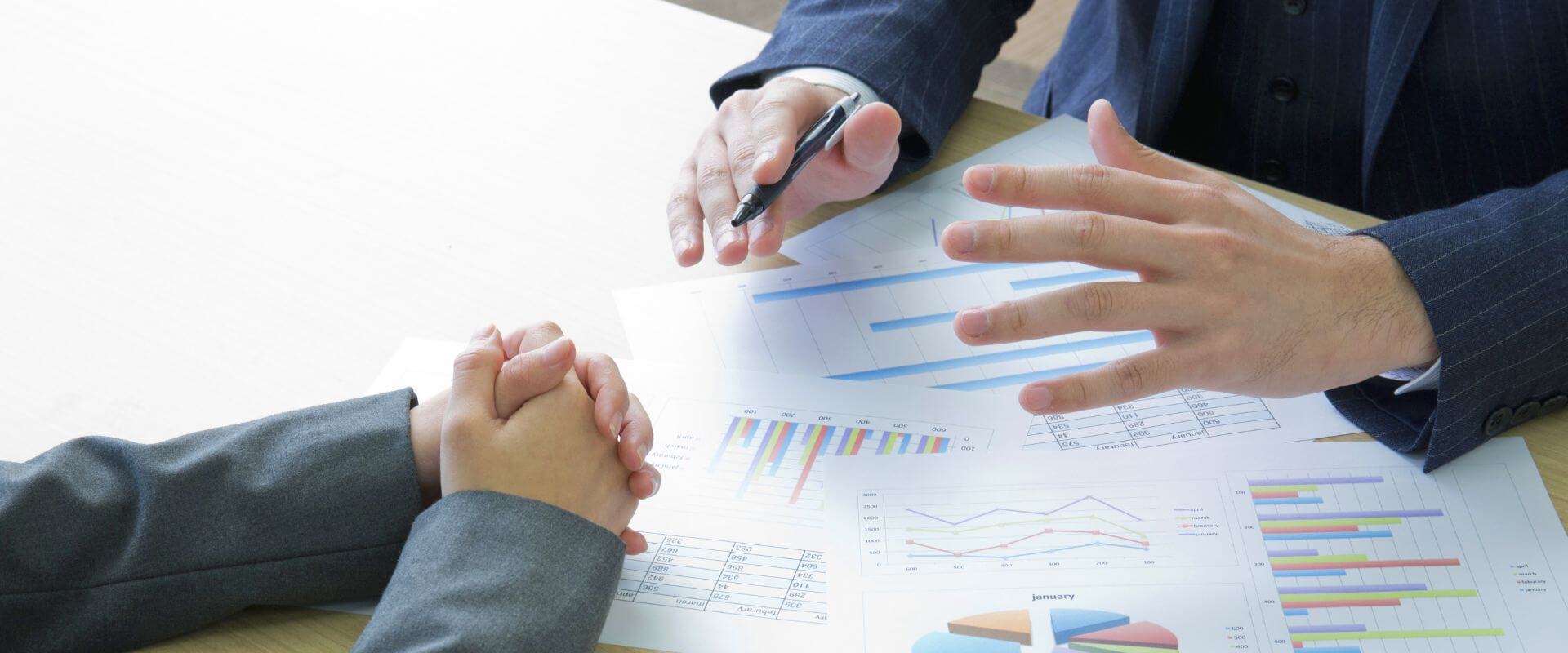
Prototype parts procurement also contributes to product development
In addition to procurement of parts for products for which mass production has been decided, members in charge of procurement of device parts also procure parts for which final specifications have not yet been decided during product development. For this reason, we do not develop products but instead participate in the same projects as a member in charge of development, meeting the product standards and component specifications requested. At the same time, we also propose parts to the development personnel, contributing to the rapid and reliable development of new products. When finalizing the standards for the final product, sometimes the specifications have to be changed, which is one of the difficulties unique to the R&D Group. But because of the involvement in the project from the development early stage, there is strong passion for the new product.
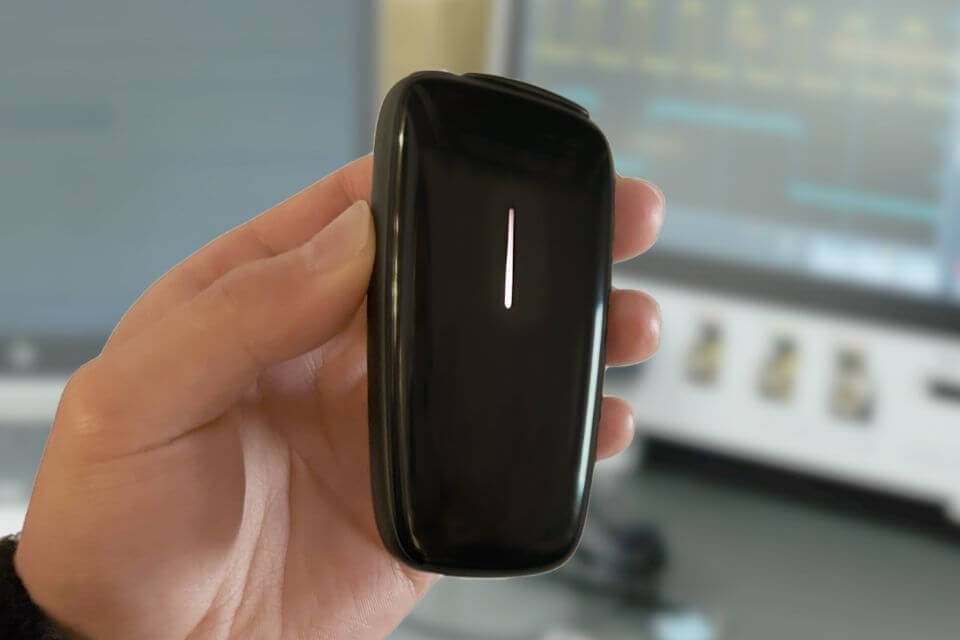
Creating a thorough management system as a gatekeeper of quality
Devices and cartridges manufactured on consignment by overseas manufacturers are transported to warehouses, where they are inspected and stored before being distributed to the market. Quality management member do everything necessary to ensure quality, including selecting inspection warehouses, designing warehouse layouts, and arranging resources such as personnel and inspection equipment. In addition to pursuing accuracy, these members also focus on operability and process improvement. There can be tough situations, such as when working with many stakeholders inside and outside the company where letting up is not an option. But working as a gatekeeper to safeguard the quality of products is rewarding work.