RRP* will continue to evolve even further, and the work to build up their quality is truly fascinating.
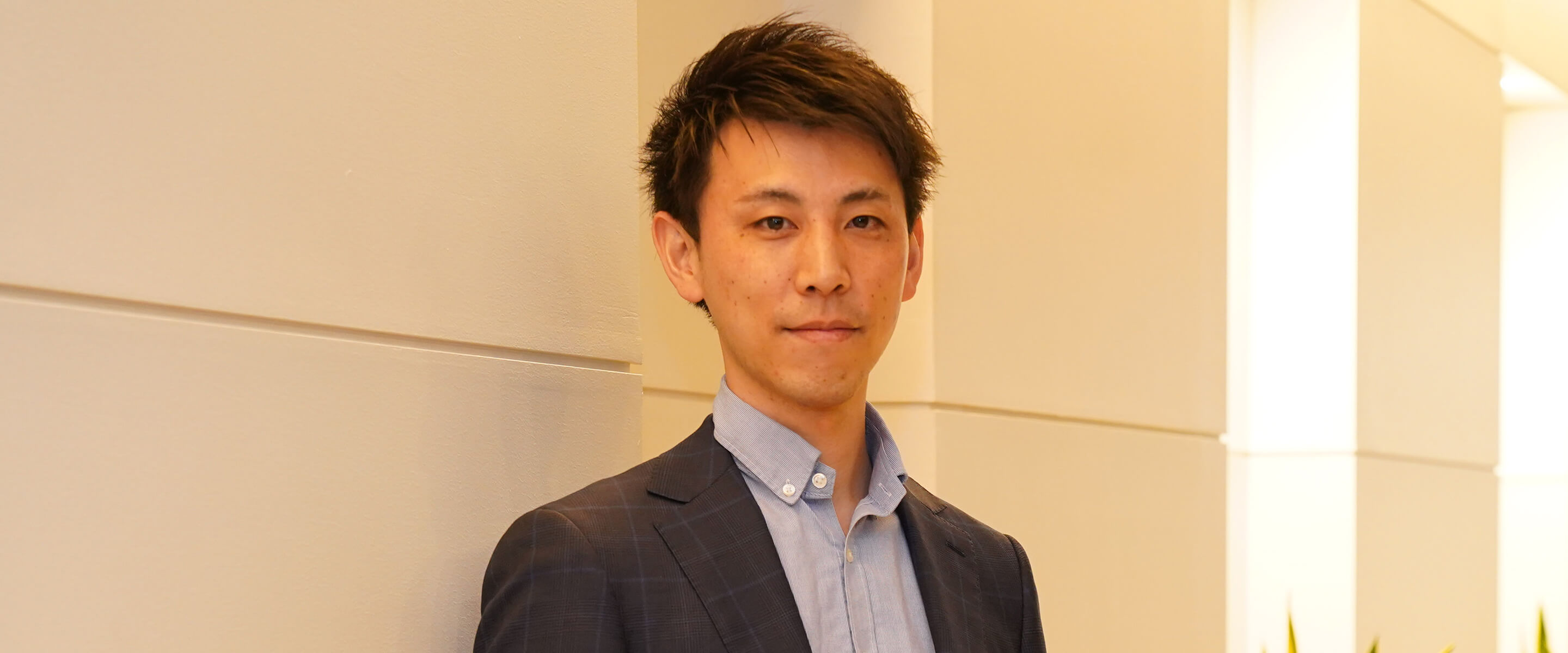
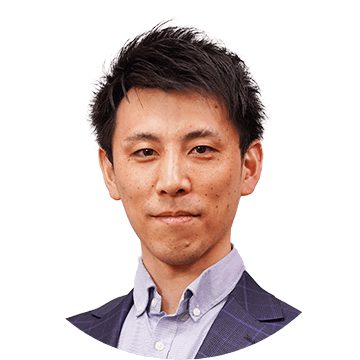
Procurement Quality Control
Hiroki Miyaoka
Quality management of devices and cartridges for RRP*
*Reduced-Risk Products: Products with the potential to reduce health-related risks associated with smoking
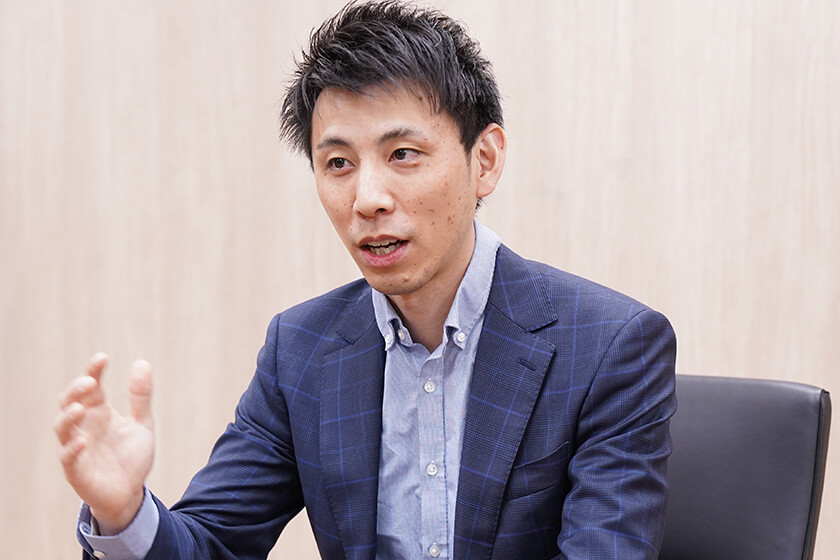
Starting from zero knowledge and experience, to build quality inspection and management systems for RRP*.
After attending a specialized vocational high school and advancing to university and then graduate school, I entered the JT Group in 2013 as a new graduate. When I started thinking about my career path after graduation, I remembered the tobacco products from the JT Group, which I had seen while traveling during my time as a student. At that time I visited several other countries, and tobacco products from the JT Group were being sold in all of them. My reasons for applying to enter the JT Group were the two points of “manufacturing” and “global business,” both of which I had a previous interest in.
After entering, I was assigned to a manufacturing plant for cigarettes, where my duties included discovering problems at manufacturing sites, and managing specific measures aimed toward improvement. I was also responsible for work such as being a point of contact for coordination with other departments and companies. The mission given to me was to raise the performance of the plant, so I focused on aspects such as improving productivity and reducing defects. In my third year after entering, I was transferred to the Quality Management Division of the plant, where I acted as a contact for communication with the Head Office that decided on various on-site measures.
In my sixth year, I was transferred to my current department. That was a time in which mass production of RRP* had just begun, so the mission of the department I was affiliated with was to carry out quality management of RRP* devices and cartridges. I was responsible for acceptance inspections at domestic warehouses for products whose manufacturing was commissioned to overseas manufacturers. This was the first time I was involved with products other than cigarettes, so I had no knowledge or understanding of devices. Selecting inspection commissioning warehouses, understanding product specifications, investigating inspection requirements and methods, performing layout and design to set up inspection processes, securing personnel and inspection equipment, and procuring materials required for work - nearly all of these procedures were completely unknown to me, so I had to create them from scratch.
*Reduced-Risk Products: Products with the potential to reduce health-related risks associated with smoking
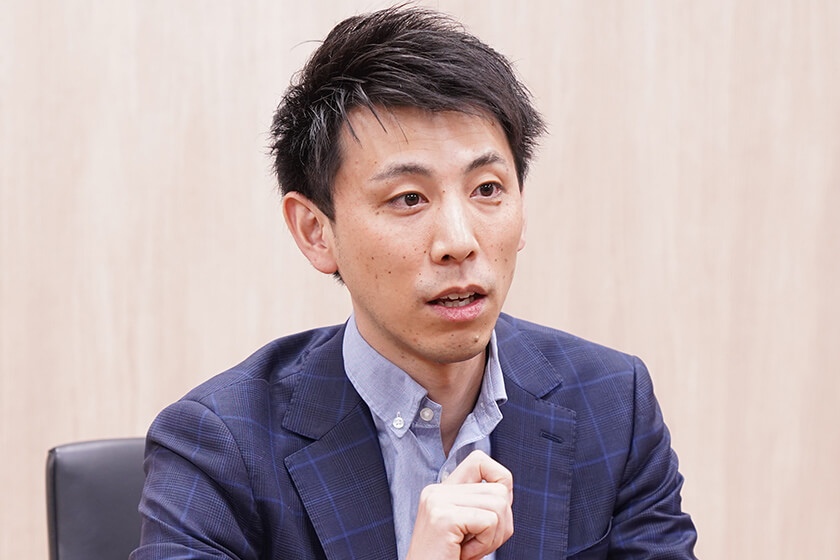
Gaining frontline experience of paradigm shifts in the tobacco industry.
Since the JT Group is a tobacco manufacturer with a long history, it possesses extensive expertise and knowledge related to cigarettes. However, RRP*, and especially their devices, is a completely new field.
We truly began RRP* manufacturing from a completely blank slate. I proceeded while receiving help from both inside and outside of the company on various matters that should be common knowledge to an electronics manufacturer, such as what requirements are necessary to ensure product quality, and what points should be kept in mind for the distribution and sale of electronic devices. For both myself and the R&D Group, it was the first project to involve such widespread coordination with other companies. Even though it was a project for the tobacco business, it felt more like starting up a venture company.
With cigarettes, the basic rules were already arranged and established, and experience and know-how were shared among employees. But with RRP*, there were no such rules related to manufacturing so we had to create them ourselves. Under such conditions, every day I created new rules and updated them whenever a non-conforming product was discovered. I continually stood at the frontlines of manufacturing in order to maintain our standards for quality, costs, and deadlines. It was my first time to work with overseas manufacturers, so it was very difficult to relate to others who had different cultures and languages, and use English (which I was not used to) to have them understand the special points for quality that were followed by the JT Group. I think everyone in my team probably felt the same way, but it was a tremendous struggle to face a mountain of tasks before us, and overcome them by solving each issue one by one.
And yet, it was very enjoyable. Every time I was faced with a problem, I investigated it, thought about it, and came up with measures to address it myself. It is not acceptable to just simply do what we are told, but it will lead to that much more motivation and joy when a product is released successfully to the world. Even now I believe that during the time of the paradigm shift from cigarettes to RRP* occurring in the tobacco industry, being able to gain experience on the frontlines was extremely valuable for me.
*Reduced-Risk Products: Products with the potential to reduce health-related risks associated with smoking
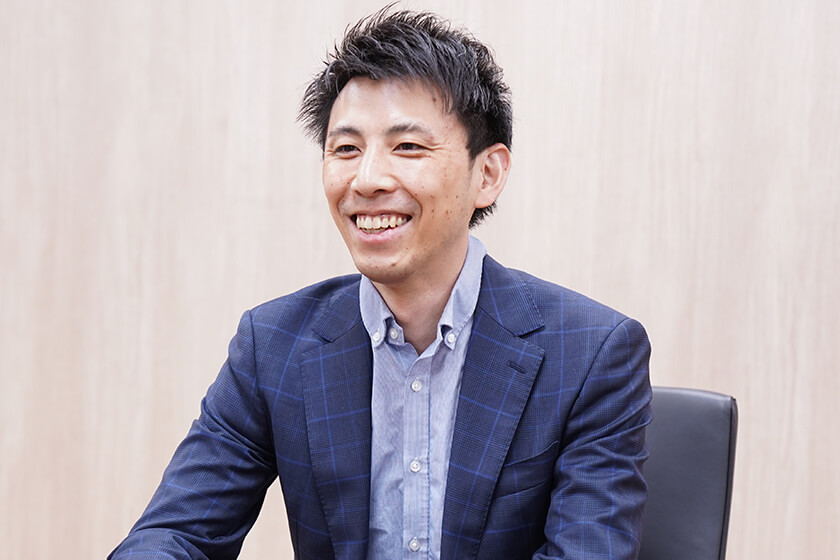
I want to unearth problems with a long-term viewpoint, and tenaciously aim to resolve them at their roots.
Personally, I want to become a global person who has a strict eye toward results, by making more active challenges through work with other countries. On the other hand, as a team member, I want to become someone who can cooperate with other members who have outstanding technical abilities, and create synergistic effects by bringing out each other’s strong points. Even though we are now continually acting like fire fighters to resolve various problems occurring one after the other at work sites, if we dig deeper and explore those problems, in the area of quality management we will find fundamental issues such as omissions or neglect of rules. I believe that quality management is not so much a matter of “compliance” or “enforcement,” but more a matter of “construction.” Making improvements requires time for thinking, and tough negotiations with external parties. I want to lead us to the goal of achieving fundamental improvements by being persistent and not giving up.
I think that as a product, RRP* will continue to evolve well into the future. In order to promote their development, I want us to raise our level of skill even more as personnel responsible for quality management. Various types of knowledge and skills related to mass production process management will be necessary to attain high-level performance related to quality, costs, and deadlines in the production of RRP*. I believe that for anyone who is interested in tobacco products, or who wishes to apply their own skills and produce great results in the quality management field, working in the JT R&D Group will bring a powerful sense of achievement.
*Reduced-Risk Products: Products with the potential to reduce health-related risks associated with smoking